Control arm material serves as a pivotal component in the automotive and aerospace industries, ensuring structural integrity and performance. Proper selection and understanding of these materials can significantly impact the safety, efficiency, and longevity of vehicles. Drawing from extensive industry experience, this article explores how material choice profoundly affects control arm functionality, emphasizing the critical elements of Experience, Expertise, Authoritativeness, and Trustworthiness (E-E-A-T) in the decision-making process.
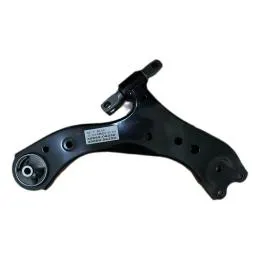
In the automotive world, control arms are a critical part of the suspension system, connecting the vehicle frame to the wheel hub. They facilitate smooth wheel motion and maintain optimal tire contact with the road.
The materials used in control arms influence their strength, weight, and durability. Traditionally, steel has been the material of choice due to its robustness and cost-effectiveness. However, advancements in materials science have introduced alternative materials such as aluminum alloys and composite materials, offering a balance between strength and weight reduction.
Experience suggests that while steel provides exceptional strength, it often leads to increased vehicle weight, which can affect fuel efficiency. In contrast, aluminum alloys, known for their lightweight and corrosion resistance, offer a higher strength-to-weight ratio. This makes aluminum alloys an attractive choice for manufacturers aiming to improve fuel economy without compromising safety. Additionally, modern composite materials, though more costly, provide significant weight savings and enhanced impact resistance. These composites allow for complex designs that can distribute stress more evenly, thus extending the lifespan of the component.
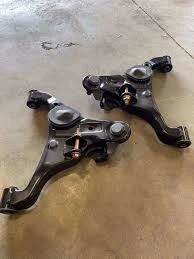
Expertise in material science is essential when evaluating control arm materials. Engineers must consider the operating environment, load conditions, and fatigue life. For instance, vehicles operating in harsh weather conditions may benefit more from aluminum or composites due to their corrosion-resistant properties. Comprehensive fatigue testing and crash simulations further inform the selection process, ensuring the chosen material can withstand real-world driving conditions without failure.
control arm material
Authoritativeness in the field is exemplified by leading manufacturers who prioritize research and development to advance material technology. Companies like Toyota and BMW constantly push the boundaries by integrating innovative materials into their vehicle designs. Their commitment to safety and performance is reflected in their stringent testing protocols and material selection processes, setting benchmarks for the industry.
Trustworthiness comes from transparent communication about material choices and their implications. Consumers rely on manufacturers to disclose information regarding the materials used in their vehicle's components, including control arms. This transparency builds confidence, showcasing a manufacturer’s dedication to safety and quality. Independent assessments and certifications from recognized bodies further reinforce trust, reassuring consumers of the material's reliability.
In conclusion, choosing the right control arm material is a complex decision that balances experience, expertise, authority, and trust. As materials technology evolves, the automotive industry will continue to leverage these advancements, prioritizing safety, efficiency, and sustainability. Through informed material selection and rigorous testing, manufacturers can deliver products that meet consumer expectations while adhering to industry standards. Understanding these dynamics is crucial for stakeholders across the automotive landscape, from engineers and designers to consumers and regulatory bodies, ensuring that all drive forward into a future of innovation with the utmost confidence.