The choice of control arm material in automotive and industrial applications is pivotal, not just for the performance of the machinery but also for safety and efficiency. This comprehensive guide delves into the world of control arm materials, exploring their types, benefits, and application-specific nuances. With years of experience in the field of material science and automotive engineering, insights from industry experts provide an authoritative and trustworthy overview of this crucial topic.
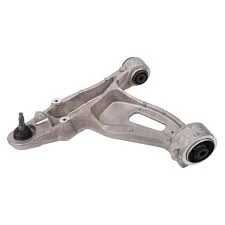
Control arms are essential components in a vehicle's suspension system, connecting the wheel hub and steering knuckles to the chassis. The material used to manufacture these parts influences their resilience, durability, and overall vehicle performance. Understanding these materials is beneficial for anyone interested in automotive design, maintenance, or even the aftermarket industry.
Traditionally, steel has been the preferred material for control arms due to its exceptional strength, durability, and cost-effectiveness. Steel control arms offer reliable performance and can withstand significant stress and strain. They are especially favored in heavy-duty vehicles and applications where enduring harsh conditions is essential. Their robustness ensures that vehicles can maneuver through difficult terrains without compromising the chassis’ integrity or the suspension system’s functionality.
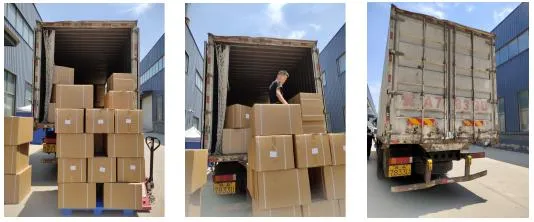
Aluminum control arms have gained popularity, epitomizing the shift toward lightweight materials in modern engineering. Aluminum is significantly lighter than steel, which reduces the vehicle's overall weight, improves fuel efficiency, and enhances acceleration. This material also boasts excellent resistance to corrosion, a crucial feature for vehicles exposed to extreme weather conditions. Aluminum control arms are often used in high-performance and luxury vehicles where reducing unsprung weight can contribute to a smoother, more responsive ride.
Forged aluminum control arms are a testament to engineering prowess. Forging enhances aluminum's natural grain structure, yielding a component that is both strong and lightweight. This process results in superior mechanical properties and is ideal for components subjected to high stress levels. As a result, forged aluminum control arms are increasingly common in racing and sports cars, where every gram of weight reduction counts toward improving speed and handling.
control arm material
Composite materials, though less traditional, are making significant inroads in control arm manufacturing. These materials, which include advanced polymers and carbon fiber composites, offer the dual benefits of lightness and strength. While these materials are more expensive, their performance advantages are compelling. Composite control arms are resistant to wear and fatigue, which makes them ideal for cutting-edge automotive applications where performance and innovation are fundamental. An added advantage is their ability to be molded into complex shapes, allowing for more aerodynamic designs that can further enhance vehicle performance.
The choice of control arm material must also consider environmental and economic factors. As the automotive industry steers toward sustainability, recyclable materials and environmentally friendly manufacturing processes are gaining traction. Steel, being highly recyclable, offers an advantage in this regard, aligning with global trends toward reducing carbon footprints and promoting lifecycle efficiencies. Similarly, advancements in recycling techniques for aluminum and composite materials are expanding their lifecycle value and environmental credentials.
Maintenance and repair also play crucial roles in determining the suitability of control arm materials. Steel, for example, while robust, is susceptible to rust and may require regular inspections and maintenance in humid environments. Conversely, while aluminum offers an advantage in resisting rust, it can be prone to damage from road debris, necessitating careful inspection routines.
Ultimately, the choice of control arm material boils down to a balance between performance, cost, and application-specific requirements. For professionals in the automotive sector, understanding these factors not only aids in making informed decisions but also enhances the safety and satisfaction of end-users.
In conclusion, as engineering continues to innovate, the evolution of control arm materials will likely lead to even more sophisticated solutions that balance strength, weight, sustainability, and cost. This ongoing development underscores the importance of staying informed about material science breakthroughs and integrating them effectively into automotive designs. The knowledge shared here is intended to empower stakeholders with the expertise needed to navigate the complexities of control arm material selection, ensuring safety, efficiency, and advanced performance in every application.