Tubular control arms have emerged as a pivotal innovation within automotive suspension systems, heralding a new era of performance and safety enhancements for vehicles ranging from daily commuters to high-performance race cars. These components, crafted with precision and expertise, play a crucial role in maintaining the structural integrity and overall functionality of a vehicle’s suspension system.
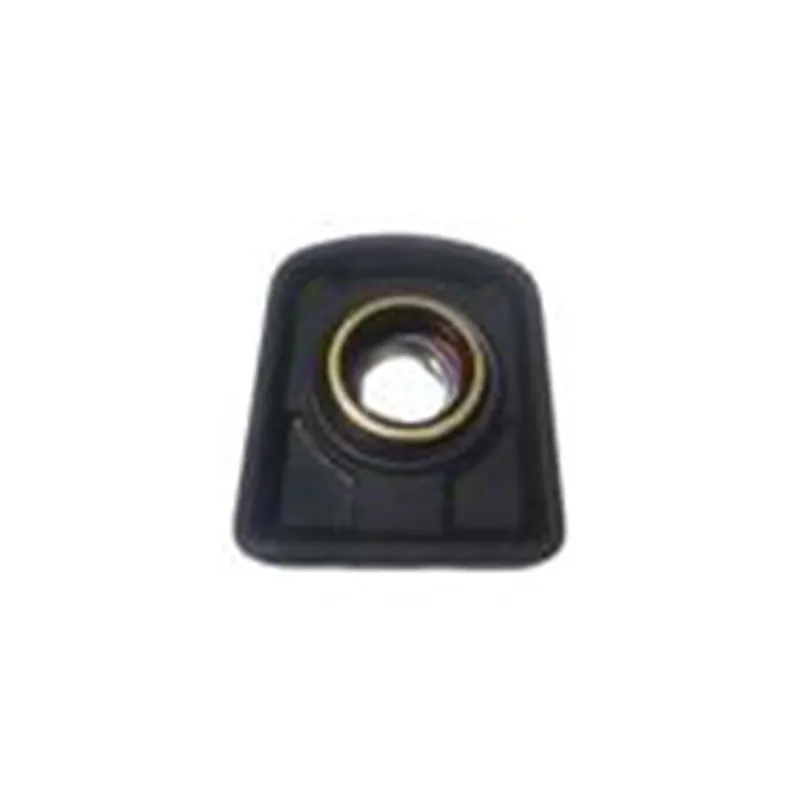
At the core of tubular control arms is their unique design, which harmoniously combines strength with weight efficiency. Unlike their stamped steel counterparts, which tend to be heavier and less flexible, tubular control arms are meticulously engineered to deliver superior strength-to-weight ratios. This advantage comes from their construction – high-quality steel tubing shaped into aerodynamic forms that not only reduce the overall weight but also enhance the suspension's responsiveness and durability. This precision engineering reduces unsprung weight, a crucial factor in improving a vehicle's handling, steering feel, and ride comfort.
Expertise in crafting these components comes from a deep understanding of metallurgical properties and advanced manufacturing techniques. Engineers employ state-of-the-art technology to ensure each control arm is produced with exacting standards, often using CAD software to model stress responses and load distributions. The manufacturing process often incorporates techniques like TIG (Tungsten Inert Gas) welding, which ensures high precision and strong, clean welds capable of withstanding the rigors of diverse driving conditions.
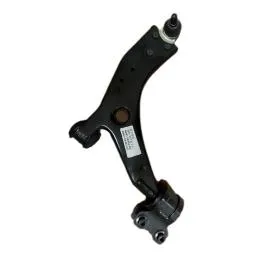
When considering the integration of tubular control arms into a vehicle, one must acknowledge their authority within suspension modification realms.
Performance enthusiasts and professional racers consistently report noticeable improvements in vehicle dynamics following installation. These components are acclaimed for providing sharper turn-in response, greater stability under load shifts, and improved tire contact—all factors contributing to enhanced driving satisfaction and safety. Such firsthand experiences underline the authoritative position tubular control arms hold in performance upgrades.
tubular control arms
Trustworthiness in evaluating tubular control arms extends beyond anecdotal evidence. Rigorous testing protocols are integral to validating their efficacy and reliability. Industry-standard tests, such as fatigue testing, simulate numerous load cycles to ensure long-term durability. Furthermore, real-world trials are conducted on racetracks and varied road conditions to verify that the performance enhancements translate outside the laboratory settings. Many manufacturers provide comprehensive warranties, reflecting their confidence and commitment to quality.
Moreover, tubular control arms are not just confined to performance vehicles; they are increasingly finding favor in everyday cars, given the rising consumer demand for improved fuel efficiency and ride quality. By reducing unsprung mass, these control arms contribute to better fuel economy—an aspect of increasing importance in today’s environmentally-conscious market. Simultaneously, they enhance ride comfort, an attribute highly valued by consumers seeking smoother, more refined driving experiences without compromising vehicle safety or handling capabilities.
In conclusion, the adoption of tubular control arms signifies a sophisticated approach to automotive suspension innovation. Recognized for their exceptional performance benefits, weight efficiency, and robust construction, these components exemplify the pinnacle of modern engineering expertise. Their credibility is further reinforced by rigorous testing, manufacturer warranties, and consistent commendations from within the automotive community. As the landscape of vehicular technology continues to evolve, tubular control arms will undeniably remain at the forefront, central to enhancing driving dynamics and advancing automotive design.